Previous slide
Next slide
About Our Amit Engineering System
Established in 2018 in Noida, Uttar Pradesh, Amit Engineering System is a trusted manufacturer specializing in Effluent Treatment Plants (ETP), Sewage Treatment Plants (STP), and a diverse range of other environmental management products. The company is committed to delivering high-quality, innovative solutions designed to meet the evolving needs of industries and communities for sustainable water and wastewater management.
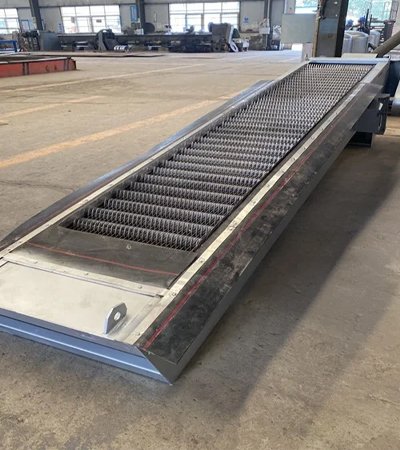
Our Products
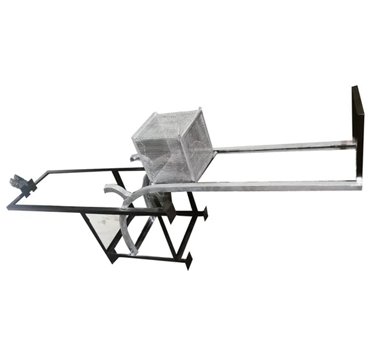
Stainless Steel Mechanical J Type Bar Screen
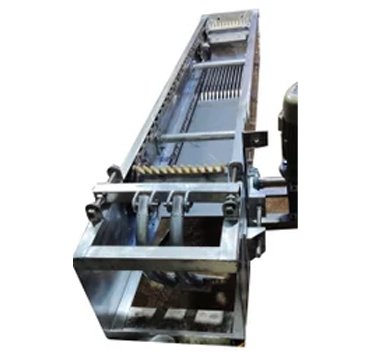
Stainless Steel Mechanical Bar Screen
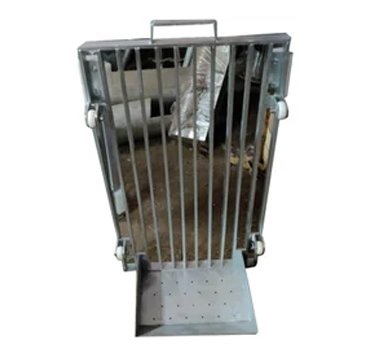
SS Steel Mechanical J Type Bar Screen
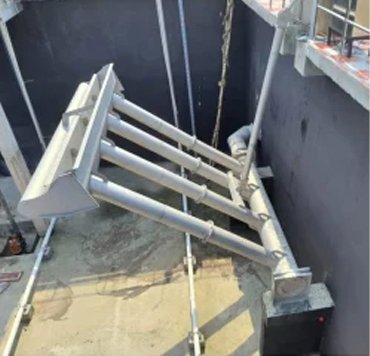
Stainless Steel SBR Moving Decanter
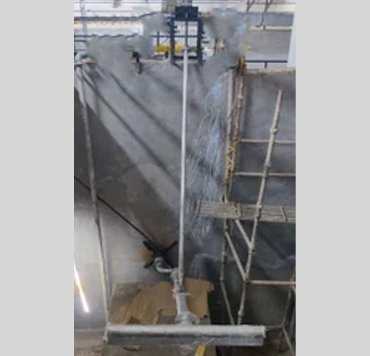
SBR Moving Decanter
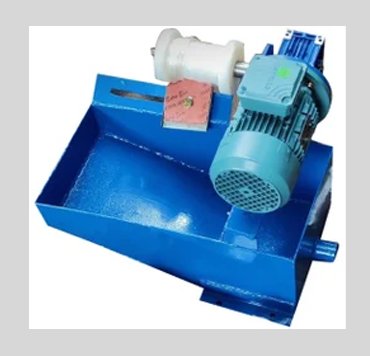
Belt Type Oil Skimmer
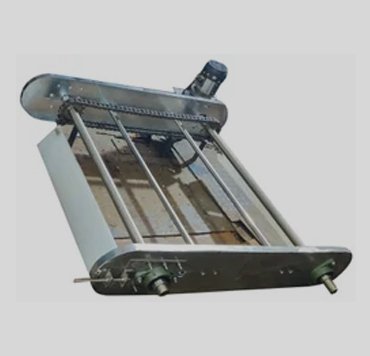
Mechanical Sludge Oil Skimmer
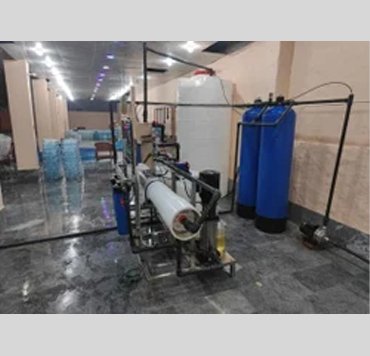
Water Treatment Plant

CLEARIFIAR MECHANISUM (HRCC)
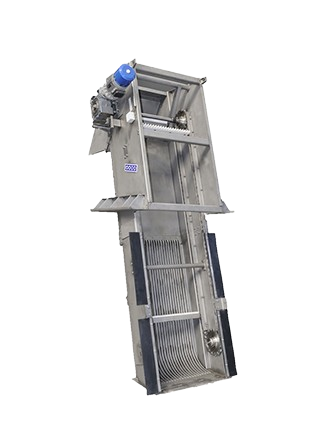
MULTI RAKE BAR SCREEN
Multi rake bar screens are made for extraction of large and medium size solid waste from effluent channel before pumping of effluent to prevent clogging of impellers of pump. The range of bar spacing can vary from 12 mm to 50 mm depending upon application of screen.
Suitable for channel depth upto 12 mtrs. And width upto 2mtrs. Screens are made of stainless steel for long service life of equipment. Material of construction-SS304/SS316
STEP SCREEN
These screens are intended for medium and small waste solids from effluent channel and recommended to be used at waste water treatment plants.
Suitable for effluent channel width up to 1200mm and depth up to 1200mm.
Automation of screens saves energy and reduces effects of human
error.
Operating principle of step screen provides formation of layer of waste solids on the top of screen bars and moves upwards to waste bin/conveyor.
Screens can be supplied with 2mm to 6mm clear gap between bars.
Material of construction-SS304/SS316
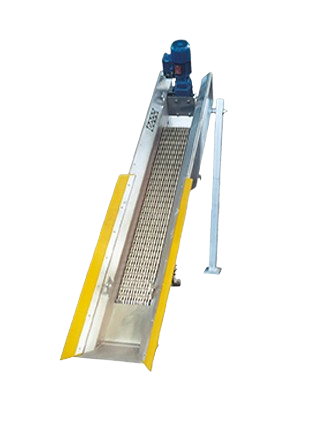
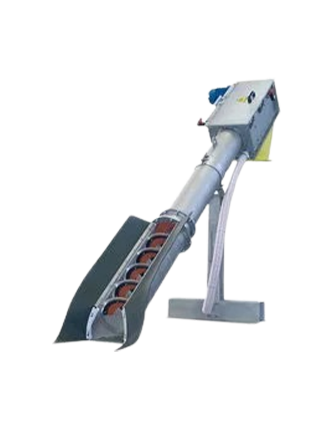
SCREW SCREEN
These screens are intended for medium and small waste solids from effluent channel and recommended to be used at waste water treatment plants.
Suitable for effluent channel width from 200mm to 600mm and depth up to 4mtrs.The perforated sheets provide high efficiency of filtration and screw is equipped with a brush on its edges to ensure cleaning of screen media in filtration zone.
The trash retaining screen is made of stainless steel in the form of perforated sheet/wedge wire screen and has larger area for filtration due to inclination in effluent channel. Waste retained on filtering screen are removed by axially rotating screw conveyor up to waste bin.
GRIT REMOVAL MECHANISM
Detritor and Classifier Mechanism (screw/rake)
The grit removal consists of two essential elements- grit collecting mechanism and grit washing mechanism. Each operates separately but in hydraulic communication with each other. The removal of grit is essential to avoid heavy deposit in pipeline and abrasion of equipments.
Mechanism
The detritor is a continuous flow tank in which the grit settles due to gravity and the water overflows through the outlet weir on the opposite side. The settled grit is scrapped by means of a scraper mechanism towards the openings on the classifier sidewall at the bottom.
The collection chamber works on velocity principle and is so designed that only grit settles down and organic matter overflows. The classifier mechanism consists of a reciprocating rake/screw driven by a gear drive fitted with a motor. The grit collected is given a thorough washing and is delivered from the top of the classifier through a chute for further disposal. The Organic Return Pump/ Mixer returns the washed organic liquor lying in the classifier back to the detritor collection chamber.
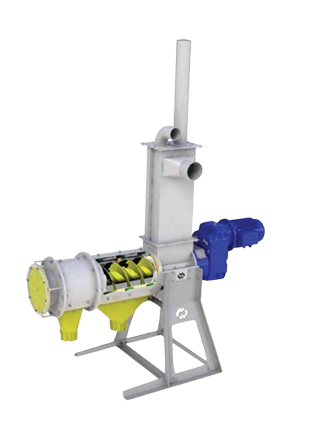
SOLID LIQUID SEPARATOR
Application: For screening and compaction of solids from mix effluent.
WORKING PRINCIPAL This separator consists a compensator tank, Seperator casing, screw conveyor and a cylindrical screen, compacted sludge outlet with variable discharge throat, separated liquid outlets, speed reducer, drive motor and machine stand. Slurry is pumped to compensator tank and it leads to separator casing, excess slurry returned to slurry tank through over flow port. The separator casing conveys slurry using screw conveyor. The liquid phase is first separated under gravity through the wedge wire mesh of casing which is covering the screw conveyor. Further material gets compressed along the path towards exit due to variable discharge throat and more liquid comes out from the solid. At discharge you will get almost dry solids. It can be further dried using dryers.
WORKING PRINCIPAL This separator consists a compensator tank, Seperator casing, screw conveyor and a cylindrical screen, compacted sludge outlet with variable discharge throat, separated liquid outlets, speed reducer, drive motor and machine stand. Slurry is pumped to compensator tank and it leads to separator casing, excess slurry returned to slurry tank through over flow port. The separator casing conveys slurry using screw conveyor. The liquid phase is first separated under gravity through the wedge wire mesh of casing which is covering the screw conveyor. Further material gets compressed along the path towards exit due to variable discharge throat and more liquid comes out from the solid. At discharge you will get almost dry solids. It can be further dried using dryers.
STP PLANT
Amit: Manufacturers of Compact Sewage and Effluent Water Treatment Plants (CETP). These plants are sustainable & environment friendly.
Our plants are valued by esteemed clients for their compact design, user friendly, durability, low maintenance, corrosion resistance and longer service life features. In order to meet the varied requirements of clients, we provide our plants in both, standard and customized forms,
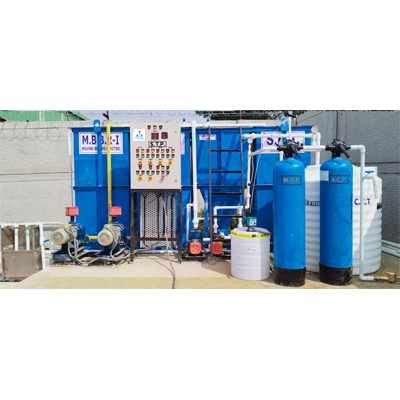
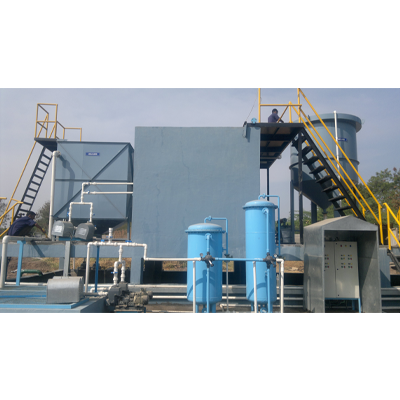
ETP PLANT
Amit: Manufacturers of Compact Effluent Water Treatment Plants. These Plants are valued by our esteemed clients for their compact design, user friendly, durability, low maintenance, corrosion resistance and longer life. In order to meet the varied requirements of clients, these products are provided in both, standard and customized forms.
ETP for the following industries: